Easy to find
Traceable samplers in quality control

Product recalls, claims for damages, damage to image - foreign bodies in products can have considerable consequences for affected companies in the food and feed sector. But numerous recall campaigns in Germany alone show that a foreign object can always accidentally get into a product. After all, the entire manufacturing process involves various hazard areas where foreign body contamination can occur - for example, through plant parts of natural raw materials, metal parts of machines or glass splinters of packaging materials.
Natural ingredients often do not pose a major risk to the consumer. Sharp-edged machine parts or packaging materials, on the other hand, can be dangerous and lead to cuts or breathing difficulties. This makes it all the more important that the end product is free of foreign matter. It is therefore important to detect possible foreign bodies at an early stage and to remove affected products before they leave the production line.
Recognizing danger points in the manufacturing process
The responsibility for a safe product lies with the manufacturer. He must ensure that the products are free from any hazardous components. A HACCP system (Hazard Analysis Critical Control Point system) helps to identify the various hazards in the manufacturing process and to initiate possible measures to limit the risks.
A major hazard in the manufacturing process is quality control. Here it can happen that when taking a product sample, the sampler or components thereof unintentionally enter production. For protection against this, detectable samplers are often used, which can be reliably detected by means of a metal detector.
Detectable stainless steel samplers

The specialist trade offers a wide range of different reusable stainless steel samplers. Samplers made of stainless steel offer the advantage that they are neutral towards many substances and there is no interaction between the sampler and the medium to be sampled. Furthermore, they do not release any components that could change or contaminate the medium. However, users should make sure that the samplers are manufactured without grooves or undercuts, as product residues or residues of cleaning agents can be deposited in them. Such residues would contaminate both the sample and the entire medium to be sampled. Furthermore, grooves or undercuts make the subsequent cleaning of the sampler more difficult.
The validated cleaning process
Easy cleaning is a decisive criterion, because quality assurance in the food and feed industry places high demands on the cleaning process. In addition to the professional cleaning of the sampler, the reproducibility of the cleaning process and proof of its effectiveness is often required. The method and the exact cleaning procedure are validated in the course of regular audits.
Depending on the sampler, however, professional and thorough cleaning can prove to be time-consuming: A trained specialist may need to disassemble the sampler before it can be cleaned of any product residues with highly effective and disinfectant cleaning agents. The sampler must then be dried and, if necessary, reassembled and autoclaved.
The required working time and the cleaning materials used cause high costs. Residues of greasy or strongly adhesive media make cleaning even more difficult, as they can usually only be removed with great effort. Toxic or dangerous material residues also pose a health risk for the cleaning specialist. In order to protect the health of the employees, appropriate occupational safety measures are essential during the cleaning process.
Cleaning is not necessary for disposable samplers

The validation of the cleaning process can be difficult and in some cases can only be achieved with elaborate measures. Some areas even completely rule out sampling with reusable samplers if their continuous particle-free and sterility cannot be guaranteed.
One alternative is disposable samplers. Unlike reusable stainless steel samplers, these samplers are disposed of quickly and easily after sampling. The validated cleaning process is thus completely eliminated. The common disposable samplers are made of plastic and are usually manufactured in a clean room, individually packed and sterilized. These are the best conditions for taking a representative sample. However, if one of these samplers accidentally enters production, it usually cannot be detected - because the plastic cannot be detected in the metal detector and the usual white colour of the material is difficult to detect even with a colour scanner.
Blue samplers are easy to find

One solution are blue disposable samplers from Bürkle. The SteriPlast® disposable samplers have a blue colour tone which does not occur naturally in food. Should one of these samplers accidentally enter production, it can be reliably detected during visual inspection or by a colour scanner due to its conspicuous colour.
A detectable version of the blue disposable samplers is also available especially for detection via metal detector or X-rays. The plastic of these samplers is enriched with metal particles. If components of the samplers come into production, they can be detected quickly and easily with the aid of metal detectors or X-rays - even though they are made of plastic. The detectable disposable samplers can therefore also be used within a HACCP system with regard to foreign bodies.
Traceable disposable samplers
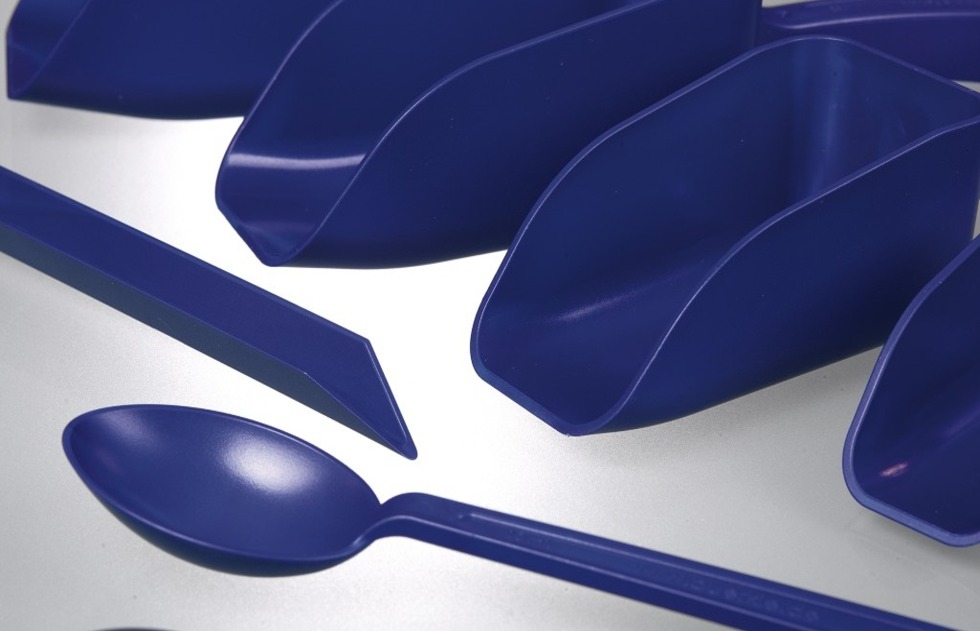
The scoops, spatulas and spoons of the detectable product line are specially designed for the removal of powders, granules, pastes and liquids. With the disposable sample scoop, a sample can be taken quickly and easily from the surface of the medium or immediately below. Thanks to the special handle design and the slightly angled front edge, the ergonomically shaped scoop can be placed horizontally - the sample does not trickle out and is safely ready for the following steps. Depending on the size, sample quantities of 25 ml to 2000 ml can be taken.
If the sample is to be taken directly from a paper or plastic bag, the use of the disposable spatula is recommended. The sampler with the long, stable handle and the pointed blade is pricked directly into the packaging bag for sampling. Separate opening of the bag is therefore no longer necessary. Close-It Food & Pharma closure seals from Bürkle can be used to securely close the puncture site. These are glued completely over the puncture site with one hand movement. In this way, the individual steps of sampling - opening and closing the packaging bags and taking the sample - can be carried out in one step.
Traceable disposable samplers
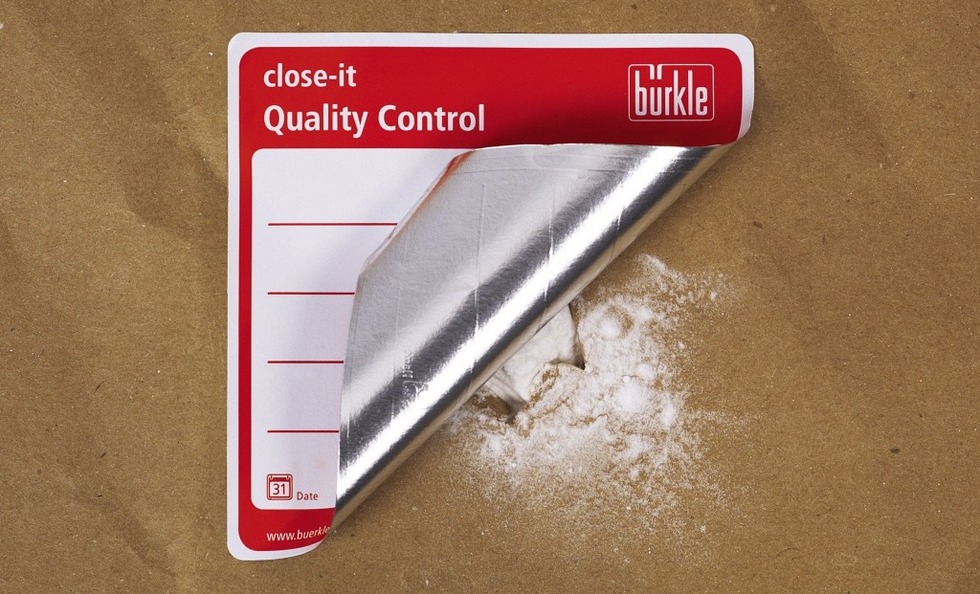
Small sample quantities can be easily taken with the detectable disposable spoon. The spoons are available in two sizes: 2.5 ml, comparable to a teaspoon, or 10 ml, comparable to a tablespoon.
All detectable SteriPlast® samplers are made of polystyrene and are produced under controlled conditions in a class 7 clean room, individually packaged and sterilized by gamma rays. The scoops, spatulas and spoons comply with EU food and FDA regulations. Contamination or cross-contamination is impossible thanks to the sterile production - and if a sampler should accidentally enter production, it can be reliably detected.
-
Article as PDF
Easy to find